Environment & Energy
Related: About this forumA Non-Ablative Composite Refractory Material Tolerant To Temperatures Up to 2000 Degrees Centigrade.
The key to high energy efficiency is the use of high temperatures - the higher the better - but the limitation is that the number of materials able to experience extreme high temperatures without being damaged is limited. High temperatures produced by primary energy - of which there is one and only one sustainable form, nuclear energy - allow for heat networks that allow for process intensification, which is the key to increased exergy recovery, and as a side factor, reduced heat rejected to the environment. This may sound paradoxical, but in fact it is actually the case.
Thus I found the paper I will reference interesting, since I have a fascination - which may or may not be realistic - with a thermochemical cycle involved in the decomposition of cerium dioxide (CeO2), at 1400°C to yield oxygen and Cerium(III)Oxide, (Ce2O3). The latter compound can be oxidized to the former by passing carbon dioxide over it, reducing carbon dioxide to carbon monoxide, which can then be reoxidized by water to give hydrogen for industrial use.
Unfortunately, I won't have much time to discuss the paper in significant detail, but here is reference to it:
Hybrid Microarchitecture-Engineered Flexible Composites with Multitemperature Adaptive Deformation for 2000 °C Thermal Protection Xiaofeng Chi, Yikai Xing, Zhe Jin, Shengtai Zhou, Zhengguang Heng, Liwei Yan, Yang Chen, Huawei Zou, and Mei Liang Industrial & Engineering Chemistry Research 2025 64 (24), 12014-12024.
An excerpt from the introduction:
In aerospace and the other complex thermal protection areas (e.g., multiple connecting elements and expandable structural gaps), there is a demand for advanced materials that combine high-temperature thermal stability, scouring and ablation resistance, and arbitrary deformation. (1−4) Both controlled deformation and ablation resistance at high temperatures are crucial to ensuring the reliability and effectiveness of flexible thermal protection materials.
Silicone rubber (SR) is a representative flexible substrate due to its high structural designability (methyl, vinyl, phenyl, epoxy modifications, etc.), heat resistance (above 350 °C), and impressive flexibility. (5−8) Despite the high-temperature oxidation resistance and ceramifiable behavior of SR, the loose and weak mechanical performance of the char layer at high temperatures is susceptible to peeling off from the surface under the erosion of airflow, consequently leading to deeper ablation. (9−11) To overcome this challenge, molecular structure modification and filler modification strategies are employed, including epoxy-modification of SR, the addition of short-cut fibers, and transition metal oxides/high melting-point ceramic fillers. (12−17) However, the high-volume fraction of fillers usually impairs the flexibility of the material as well as reduces the deformability. On the other hand, high ablation-resistant flexible materials which exhibit low coefficients of thermal expansion are mostly used as gaskets in passive compression for heat protection, failing to meet the needs of heat sealing and thermal protection of expanding gap areas.
In ablative environments, the expanding gap causes a continuous increase in temperature at the area, and accordingly, there is a demand for material that senses the temperature change and adaptively changes itself to achieve gap sealing and thermal protection. Thermal-responsive deformable materials have received extensive attention, such as hydrogels and shape memory polymers. (18−20) Hydrogels change shape depending on the swelling ratio at different temperatures, but the water as the medium limits their application in ablative conditions. (21) The structural design of reversible and fixed phases of shape memory polymers allows for a wide range of response temperatures. However, they do not possess active adaptive properties to accommodate the expansion of gaps. (22) Although these smart deformable materials demonstrate excellent thermal response performance, poor thermal stability has constrained the development of smart deformable materials at extremely high temperatures.
The National Aeronautics and Space Administration proposed a baseline sealing structure consisting of an alloy spring skeleton and an intermediate filling of heat-resistant felt, which is suitable for thermal protection of moving parts. (23,24) However, the heat impact of up to 1600 °C reaches the limits of the material. Dunlap et al. found that the baseline sealing structure was prone to yield and lose elasticity at elevated temperatures. (25) Therefore, the simultaneous organization of high-temperature oxidation resistance, ablation resistance, and controllable adaptive deformation in flexible materials remains a formidable challenge.
In this study, a strategy to simultaneously achieve high ablation resistance and multiple temperature-responsive deformations in a flexible matrix was proposed. The key lies in the preparation of a graphite intercalation compound (GIC) with specific temperature-responsive expansion and the use of commercially available expandable microspheres (EM), allowing for continuous adaptive deformation over multiple temperatures.
The material in question is a mixture of graphite, silanes, ZrB2, iron oxides, and carbon fibers.
Upon exposure to extreme heat, the following chemical reactions are said to take place:
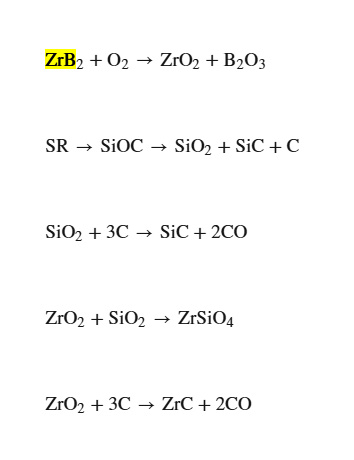
The authors write:
The high-temperature ceramics reinforced the char layer to resist scouring because mechanical property was a key indicator to determine resistance under hyperthermal environment. (31) A compression test was performed on the char layers by means of a probe with a diameter of 2 mm, showing the evolution of the force required for the puncture. It was worth noting that the adaptive composite endured a maximum pressure value of only 5 N, whereas ZrB2 modified composite attained a peak pressure value of 30 N, improving by 600%...
A figure from the text:
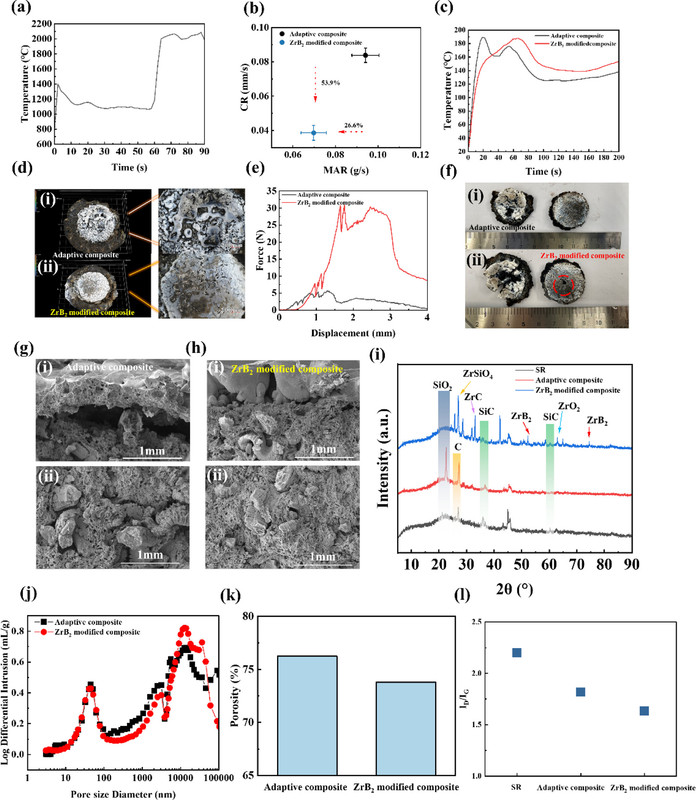
The caption:
From the conclusion:
Cool. I mean, Hot. Both.
Enjoy the weekend.